例2 流体温度变化引起流量测量误差
青岛某厂的一台220t/h锅炉,发汽流量和进水流量均用孔板流量计测量,锅炉长期以来一直满负荷运行,但有一个不解之谜,即发汽流量总是比锅炉进水流量与减温水流量之和高2%左右。照理说根据差压式流量计测量结果计算出来的平衡差能达到≤2%已属不易,但运行人员仍不满意。于是仪表人员对孔板计算书进行复算,对各台仪表进行复验,对仪表安装进行检查均未发现问题。最后要求仪表制造厂作解释。于是有关人员对这两个测量系统方方面面的情况作了较全面的调查。最后,当问及流体实际运行工况同孔板计算书中的设计工况是否偏离时,运行人员解释除氧水温度因故比设计条件低50℃,而这一偏离在进水流量表中既未作相应的修正,也未引入温度补偿。由于温度的这一偏离,使流体实际密度增大4%,进水流量计偏低2%是理所当然的事。
例3 液体温度升高,体积膨胀,体积流量相应增大
江苏某化工厂两台DN100电磁流量计分别测量两根管道的两种稀酸,汇合后进入总管,并由DN200mm电磁流量计计量总流量。使用单位向仪表制造厂反映总表流量为分表流量之和的120%~130%,认为3台仪表均不准确。经现场了解,管道压力为0.6MPa绝对压力,两分管液体温度为30℃,混合液体进入总表前经反应器热交换,温度升高到180℃。假定稀酸的温度体积膨胀系数与水相近,从30℃升高到180℃体积增加约12%,可判定总表和分表总和之间读数差主要是液体温度变化所致。此外,0.6MPa绝对压力158.5℃水已开始沸腾,流过总表的流体,在液体中夹有部分蒸汽,亦会增加总表体积流量的读数,可认为找到了总表读数多20%~30%的原因。
④用冷凝水量验证蒸汽流量计的准确性。有许多蒸汽用户是取用蒸汽中的热量,此蒸汽经过流量表计量后送用热设备,蒸汽放出热量后变成质量相等的冷凝水,然后从疏水器排出。将一段时间内的冷凝水收集起来,测量其质量,然后与同一段时间内蒸汽表所计的总量比较,验证蒸汽表的准确性。这种方法是在流量计安装使用现场经常使用的简单而易行的方法,但应注意下面两点。
a.冷凝水在排出疏水器时总要夹带少量的蒸汽,进行总量比较时应予考虑,最好是将疏水器排入装有适量冷水的容器底部,从而使残余的蒸汽全部变成冷凝液后再测量。
b.如果流经流量表的是饱和蒸汽,必须考虑其中夹带的水滴对平衡计算的影响。现在使用涡街流量计测量蒸汽流量的方法应用十分普遍,而涡街流量计对蒸汽中的水滴基本不响应,而在疏水器的排出液中却包含了这些水滴,因此,如果蒸汽的湿度为5%,那么冷凝水总量比蒸汽流量表所计的总量高5%则属正常。困难的是蒸汽的湿度究竟是多少难以测量。只知道在进流量计之前,如果管道上装有疏水器,则可将分层流动的水排放掉,这时蒸汽中的水滴含量约为0~5%(质量比)。
⑤运用物料平衡法时应注意的问题
a.仪表的安装应符合规程要求,如果因现场条件限制无法完全满足,则在核算时应对由此引起的误差作出评估。
例4 一幢大楼的低区冷冻水系统(见图6.25)流量测量总表与各分表示值之和差5%
该系统共有12台分表,管径从DN80~DN200,均用WSF型电磁流量计测量流量,而总管为DN600,采用WSTDS型夹装式超声流量计测量流量。供水温度和回水温度也接入二次表,以实现对冷量的计量。总管流量计HIQ01由于管径大,对直管段要求高,现场无法满足要求,前直管段只能勉强达到5D,仪表投运后发现总管流量示值比各分管流量示值低5%。
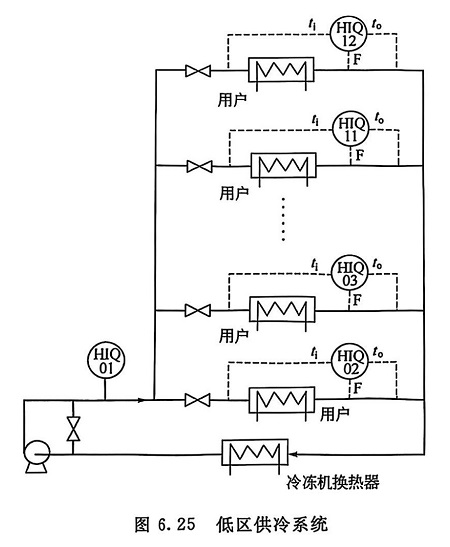
在作系统误差分析中,工作人员核对了各分表的数据设置和各台表所对应的用户的设备能力,确认流量示值可信。尤其是该型号电磁流量计精确度较高,其基本误差限为±0.3%R,因此初步判定5%的量差主要是由于总管流量计误差大引起的。
在分析直管段长度不够对超声流量计示值影响的过程中,三条曲线(见图6.21)都表明夹装式单声道超声流量计在直管段不够长时示值偏低,在前直管段长度为5D时,示值约偏低5%。从而使总表与分表计量差的矛盾找到了答案。
b.防止流体倒流导致重复计量而引入误差。
例5 间歇发料系统(见图6.26)停泵期间泵出口外管内存料返回到泵的进口
上海某氯碱厂用泵将料液从一个部门打到另一个部门,输送量由一台智能电磁流量计测量。当一批料输送完毕泵即停止运转,于是泵出口外管内的料液返回泵的进口。由于外管直径大,线路长,所以每次返回量较大。一段时间只发现流量计所计总量比储槽中用容积法所计总量大,但原因不明。后来检查中调阅智能流量计所保存的总量值,才明白问题所在,该仪表中保存的总量值有三个,即正向总量QD、反向总量QR以及正反总量之差Q=QD-QR结果储槽中用容积法所计总量值与Q基本相等,于是电磁流量计面板显示总量指定为Q,问题得到解决。
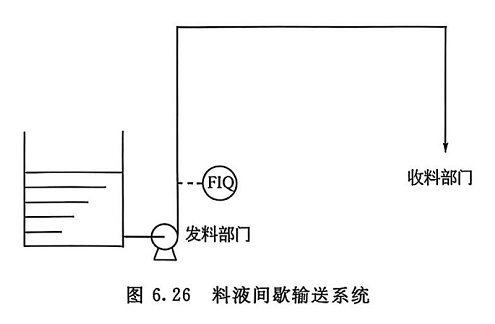
例6 并联运行的两台锅炉产汽流量重复计量(见图6.27)
某公司有两台并联运行的全自动燃油锅炉,其中一台A正常发汽,另一台B作热备,两台锅炉的汽包出口管上均装有涡街流量计,经计量的蒸汽送分配器。发汽总量和耗汽总量统计中发现发的量多耗的量少。经仔细观察发现处于热备状态的锅炉,其汽包所耗散的热量取自正常发汽的锅炉,不仅如此,由于分配器压力总是有些波动,在分配器压力降低时,锅炉B汽包对分配器供汽,流量计计出供汽量。在分配器压力升高时,分配器对锅炉B汽包充汽,这部分汽也是经常有变化,重复计量也经常发生,最后导致总表所计总量(FIQ01和 FIQ02 所计总量之和)明显高于耗汽总量。而且压力波动幅值越大,越频繁,总表所计总量偏高越多。
在工厂煤气发生站也有类似的情况,煤气连通管压力升高时,系统对停用发生炉的气容充气,煤气连通管压力降低时,停用发生炉的气容对系统“供气”,仪表计出“供气”量。
(2)热量平衡法 将与被测流量相关联的有关数据代入热量平均方程式,计算出流量理论值,用以验证流量计示值,这是仪表工程师们常用而有效的验证方法。
除氧器顶部排放氧气的时候还要带走少量蒸汽,排放量以加热耗汽量的3%计,则除氧器总汽量应为1404kg/h。
本例计算是建立在除氧器送出的除氧水全部进入锅炉并全部变成蒸汽这一基础上,因此汽水系统不能有泄漏,测试期间不能排污,而且汽水采样损失的水量作忽略不计考虑。如果采样量较大而不容忽略,则应对损耗量作一测试或估算。
(3)设备能力估算法
根据设备能力来估算流量是个“古老”的方法,早在几十年前,煤气公司就用煤气压缩机开机台时作为输送煤气的计量手段,直到有了较先进的煤气流量计的现在,这一方法仍作为监视、核对流量计示值的手段。
运用该方法时,应注意下面各点。
a.压缩机出口压力应为规定值,因为出口压力不同,压缩机的内泄量也相应变化。如果达不到规定值,应计入此因素对排气量的影响。
b.设备的效率同其完好状况密切相关,在其完好状况不佳时,输出流量相应减小。
c.压缩机毕竟不是计量器具,它没有计量准确度的概念,同一种型号同一个规格的压缩机,在规定的条件下考核,排气量也允许有-5%~+10%的差异。多年来人们沿用这一方法,一是煤气压缩机出现得早,在其投入工业应用时还没有合适的流量计可选用;二是有“定排量”的概念,即压缩机每旋转一周或每往复一次,就有固定量的气体被吸入和排出;三是因为出口压力很低,机内泄漏可以忽略,在其他类型的压缩机上,因为出口压力较高,机内泄漏受多种因素影响,仍使用这个方法不够可靠。
将这一方法引申到泵上,也应区别对待,因为泵的种类很多。对于齿轮泵,属正排量类型,用其铭牌上所标的输送流量数据作参照,意义较大,但应考虑出口压力、流体黏度和齿轮新旧程度对机内泄漏的影响。出口压力越高、流体黏度越小、齿轮磨损越严重,机内泄漏越大。对于离心泵,其铭牌上所标的输送流量数据基本上不能用作验证流量计示值的依据。下面的三个例子都是由使用单位用离心式水泵铭牌数据验证流量计示值和由于对水泵的特性认识不深而引发的误解。
例8 两台同规格水泵由于实际性能差异引发的误解
某水厂两台同规格水泵输给两条管线,分别装有DN600mm电磁流量计,布置如图6.28 所示。该水厂运行人员从泵铭牌上的额定流量来核对仪表读数,称泵A通A表(即关闭阀C)仪表误差为+(10~15)%,泵B通B表误差为-5%,认为两台仪表均不准确。技术当即利用装有阀C的有利条件,试测泵A通B表和泵B通A表的流量,得出与上述相近的数据。两台流量计测出同一台泵的输水量相近,证明除管网负载有些差别外,主要是两台水泵性能上的差异。
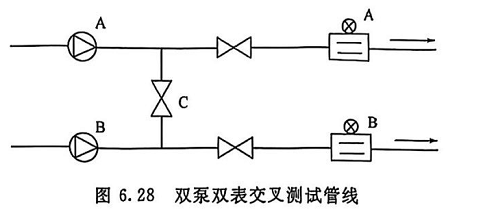
例9 扬程差别大的泵并联运行误认为流量仪表间相互干扰
吉林某厂用几台泵并联输送液体,每台泵的下游各装有电磁流量计,然后汇集总管输出。各泵单台运行(或其中几台并联)都很正常,但增开某一台泵并入管系,原来运行各泵的仪表指示流量明显减少,甚至出现指示反向流现象。运行人员认为该特定泵所装电磁流量计干扰了其他运行中的仪表。经检查确认为仪表正常,找出产生这一现象的原因是所增开泵的扬程比其他高得多,致使压抑低扬程泵的输出,使之减少,甚至倒流。
例10 多台同规格泵并联运行输出量变化的误解
河南洛阳某水厂A、B两泵房如图6.29所示,各装有同规格水泵7台,各自汇集到 DN700mm总管输出。总管上各装有一台电磁流量计,在流量计下游两总管接有连通管和闸阀,平时此闸阀全开。试开动两泵房不同台数的泵,得出如表6.3所示流量计上读数。将A、B两泵房开泵台数对调,所得读数亦相接近。水厂运行人员认为流量仪表线性不好,低流量时指示偏低,似乎开泵台数增加,出水量应按比例地增加。实际不然,这是一种误解,在表6.3所列的数据中,除了试验序号4中B泵房开了一台泵,而流量计读数却为零一项,可能是由该台泵存在问题而引起,其余各项数据同预计的一致,都是由于对离心式水泵输出特性认识有出入而引起的。其实,离心式水泵的输出流量同其出口压力有对应关系,出口压力越低,输出流量越大,反之则小。多台离心式水泵并联运行时,瞬间停掉其中的一台泵,则继续运行的各台泵出口压力下降,输出流量增大。
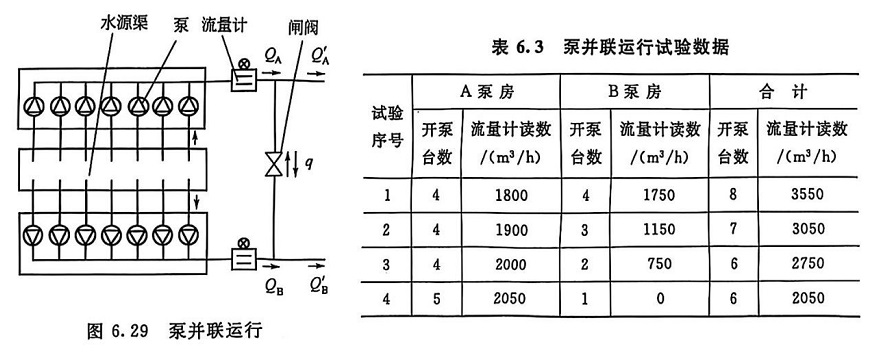